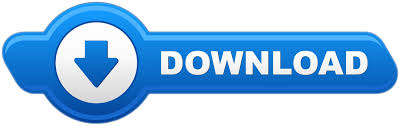
I think Paul intended $30 to be used differently, but like being able to interrogate Gcode and knowing the darkness level based on S level is aligned.Īlso LB, Picengrave, and I believe a lot of commercial SW align the DPI based on line interval (scan interval). Thus set 255 for both $30 and Smax and adjust power/speed in LB. I quickly found that the $30 and Smax are not integers so fractional values (floats) are interpreted fine. Quote from tprothma on January 13, 2019, 3:08 pm and sharing. Please share back once you've made progress. Understanding the fundamentals has been a tiresome chore, but I'm a knowledge seeker so I roll up my sleeves and hammer away at a problem. My eye for a good pre-processed image and a good engraving has improved, yours will too. The limitation was the dynamic response of the C02 laser and went to a laser diode. Paul's controller is in fact Awesome! I just ran out of steam with C02 lasers as the limitations are not the controller. LB lacks some knobs I like for getting a good range as I'm trying to do photographic quality engravings.
Photograv tutorial software#
I've written special python code to take a high end image conversion software output and do unidirectional engraving. Attached is one I created which each box is 5x1omm and the text is vector based text, then converted to a raster image directly.Ħ) If you suspect backlash on your machine, deselect Bi-directional. The correct combination will give you dark and light with nice range in between.ĥ) Start with a greyscale image and get it looking nice, then use your target image. Setting incorrectly in either direction will look make the image lose clarity.Ģ) Align $30 and Smax, this ensures the Controller is interpeting the Gcode properly.ģ) Fix max power at some relative low value (guessing between 10% and 20%) and set min to 0% this means whites do not get burned.Ĥ) Sweep speed until you find the right speed based on that power.
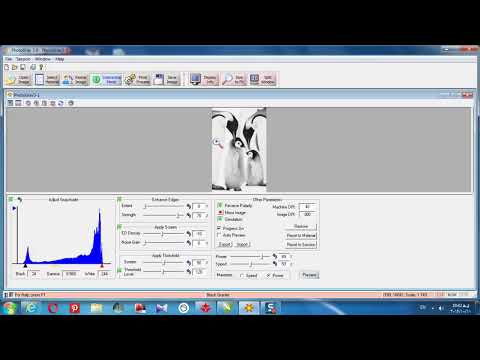
too big and there will be gaps between the lines, too small and there will be overlap. Someone may be able to give you more precise combinations for our machine, but I've been working on a diode laser and these are the basic anchoring points (independent of machine):ġ) Figure out the machine's Line Interval (based on optics for K40).

Hopefully it's making sense how things are linked. If still over burn at the maxed out speed, then bring down the power. My disclaimer is that I've not done this on the K40, so I don't know if 10% has an achievable speed or whether we will max out the speed and still overburn. If it's overburning (digging into the material, run the speed faster). Probably start with something like 20mm/s. Then start sweeping speed and find the correct speed for the assigned power which gives a good greyscale. This 10% (relatively low) power setting is because the 40W laser is more than enough power to burn the top of the plywood. This means a black dot would be set to 26 (10% of S max)and a white dot is zero. Then set min power to 0% and max power to probably 10%. Now everything is basically aligned (this is not optimizing the granularity, but easiest to understand so I recommend starting with that). In LB go to Edit->Device Settings and set S value max to 255. Set $30 to 255, set $31 to 0, you do this in the console window of LB, $$ to confirm they were set.
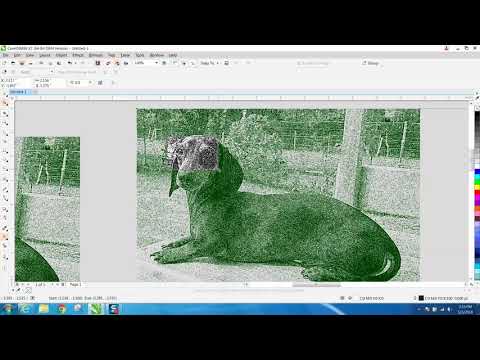
White will give a power of 0, and black will give a power of 255. Greyscale images are processed in LB as 8bit, so there are only 256 distinct values. This also eliminates variabilities with respect to your image. I had to create my own greyscale that has never been converted to jpg (only a BMP) which will add anomalies due to compression.

Start with a greyscale test pattern I've attached. Min dot size: This is based on optics as 16 microsteps is more than enough res for our steppers.
Photograv tutorial full#
Photograv uses dithering for which is only on/off (1bit) and not needed for Paul's controller which has full PWM control. For a properly processed image I see no reason to set min to anything other than 0%. I've been doing a lot of engraving with a laser diode, so I have not fully characterized the ideal settings for the K40. Quote from tprothma on January 13, 2019, 2:34 am
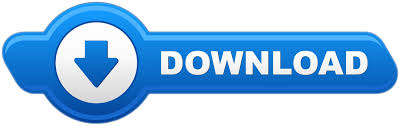